Products - Panels for OEM users - boilers
Following are the OEM application in which Control Systems Engineers have devoted many years in development
Wind Energy / Wind Turbine Panel | Compressor Control Panel | Flare Systems | Incinerators | Evaporators |
Filtration systems | Boilers | Chillers | Spray Driers | Krom Schroder | Test / Simulation | Transfomers | HVAC Panel
Filtration systems | Boilers | Chillers | Spray Driers | Krom Schroder | Test / Simulation | Transfomers | HVAC Panel
I. INTRODUCTION
Over the years the demand for high quality, greater efficiency and automated machines has increased in the industrial sector of power plants. Power plants require continuous monitoring and inspection at frequent intervals. There are possibilities of errors at measuring and various stages involved with human workers and also the lack of few features of microcontrollers. Thus this paper takes a sincere attempt to explain the advantages the companies will face by implementing automation into them.
The boiler control which is the most important part of any power plant, and its automation is the precise . In order to automate a power plant and minimize human intervention, there is a need to develop a SCADA (Supervisory Control and Data Acquisition) system that monitors the plant and helps reduce the errors caused by humans. While the SCADA is used to monitor the system, PLC (Programmable Logic Controller) is also used for the internal storage of instruction for the implementing function such as logic, sequencing, timing, counting and arithmetic to control through digital or analog input/ out put modules various types of machines processes. Systems are used to monitor and control a plant or equipment in industries such as telecommunications, water and waste control, energy, oil and gas refining and transportation.
II. DRAWBACK OF CONVENTIONAL SYSTEM
Conventional equipment systems are prone to errors due to the involvement of humans in the data collection and processing using complicated mathematical expressions. Thus what we require is a system that collects raw data, processes it and presents it in values which can be verified and compared with the standard values. In the coding process of this implementation with micro-controller, it requires a fast and efficient processing which on the other part depends on the length and sub-routines of the coding process. Thus it provides a real challenge with systems involving
III. METHODS
All the values can be filled up by the introduction of the automation technique into the power plants. The automation technique involving the automatic control of all the processes which includes the monitoring and inspection needs provides for a very efficient system. The automation process helps the company having the power plant to reduce the amount of errors that occur , reduction in the human resources, increased efficiency, and most importantly very cost effective.
IV. CRITICAL CONTROL PARAMETERS IN BOILER
A. Level Control
Steam Drum level, De-aerator level and hot well level
B. Pressure Control
Force draft pressure, Induced draft pressure, Steam drum pressure, Deaerator pressure, Turbine inlet steam pressure, balanced draft pressure
C. Flow Control
Air flow, Steam flow, Water flow
D. Temperature Control
Deaerator temperature, Steam drum temperature, Underbed boiler temperature, Turbine inlet steam temperature, Flue gas temperature.
V. AUTOMATION
Delegation of Human Control to technical Equipment aimed to wards achieving. Advantages Higher productivity, Superior quality of end product, Efficient usage of raw materials and energy, Improved safety in working condition.
Over the years the demand for high quality, greater efficiency and automated machines has increased in the industrial sector of power plants. Power plants require continuous monitoring and inspection at frequent intervals. There are possibilities of errors at measuring and various stages involved with human workers and also the lack of few features of microcontrollers. Thus this paper takes a sincere attempt to explain the advantages the companies will face by implementing automation into them.
The boiler control which is the most important part of any power plant, and its automation is the precise . In order to automate a power plant and minimize human intervention, there is a need to develop a SCADA (Supervisory Control and Data Acquisition) system that monitors the plant and helps reduce the errors caused by humans. While the SCADA is used to monitor the system, PLC (Programmable Logic Controller) is also used for the internal storage of instruction for the implementing function such as logic, sequencing, timing, counting and arithmetic to control through digital or analog input/ out put modules various types of machines processes. Systems are used to monitor and control a plant or equipment in industries such as telecommunications, water and waste control, energy, oil and gas refining and transportation.
II. DRAWBACK OF CONVENTIONAL SYSTEM
Conventional equipment systems are prone to errors due to the involvement of humans in the data collection and processing using complicated mathematical expressions. Thus what we require is a system that collects raw data, processes it and presents it in values which can be verified and compared with the standard values. In the coding process of this implementation with micro-controller, it requires a fast and efficient processing which on the other part depends on the length and sub-routines of the coding process. Thus it provides a real challenge with systems involving
III. METHODS
All the values can be filled up by the introduction of the automation technique into the power plants. The automation technique involving the automatic control of all the processes which includes the monitoring and inspection needs provides for a very efficient system. The automation process helps the company having the power plant to reduce the amount of errors that occur , reduction in the human resources, increased efficiency, and most importantly very cost effective.
IV. CRITICAL CONTROL PARAMETERS IN BOILER
A. Level Control
Steam Drum level, De-aerator level and hot well level
B. Pressure Control
Force draft pressure, Induced draft pressure, Steam drum pressure, Deaerator pressure, Turbine inlet steam pressure, balanced draft pressure
C. Flow Control
Air flow, Steam flow, Water flow
D. Temperature Control
Deaerator temperature, Steam drum temperature, Underbed boiler temperature, Turbine inlet steam temperature, Flue gas temperature.
V. AUTOMATION
Delegation of Human Control to technical Equipment aimed to wards achieving. Advantages Higher productivity, Superior quality of end product, Efficient usage of raw materials and energy, Improved safety in working condition.
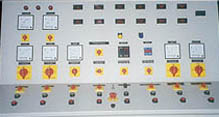